How to Choose a Reliable 24V 60Ah Forklift Battery Wholesale Supplier?
A 24V 60Ah forklift battery is a rechargeable power unit designed for electric forklifts and industrial vehicles. It delivers 24 volts of direct current (DC) with a 60-ampere-hour capacity, providing extended runtime for material-handling equipment. These batteries typically use lead-acid or lithium-ion technology, with lithium variants offering faster charging, longer lifespan, and reduced maintenance compared to traditional options.
Key considerations include supplier certifications (ISO 9001, UN38.3), production capacity, and after-sales support. Evaluate battery cycle life (minimum 1,500 cycles for lithium), warranty terms (3-5 years standard), and compatibility with charging systems. Reputable suppliers like Redway Power offer UL-certified batteries with integrated battery management systems (BMS) for thermal protection and charge balancing.
When evaluating suppliers, verify their testing protocols for vibration resistance (MIL-STD-810G standard) and shock absorption. Top manufacturers conduct 72-hour formation charging cycles to optimize plate conditioning. Request third-party cycle test reports showing capacity retention after 500+ charges. For large orders, prioritize suppliers with automated production lines capable of 10,000+ unit monthly output.
Supplier Attribute | Minimum Requirement |
---|---|
Cycle Life Certification | 1,200 cycles @ 80% DoD |
Charge Efficiency | >95% for lithium-ion |
Delivery Lead Time | <15 working days |
Technical Support | 24/7 remote diagnostics |
What Safety Standards Govern Forklift Battery Production?
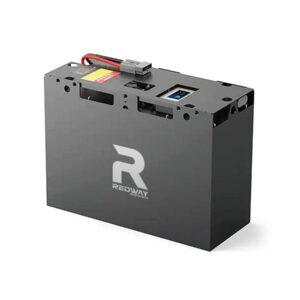
Compliance with IEC 62619 (safety for industrial batteries), UL 2580 (traction batteries), and ISO 3691-4 (material handling) is mandatory. Premium suppliers exceed these with IP67 ingress protection, CAN bus communication for real-time monitoring, and flame-retardant casing (UL94 V-0 rating). All shipments require UN38.3 certification for lithium battery transportation safety.
24V 200Ah LiFePO4 Forklift Battery
Advanced manufacturers implement multiple protection layers including pressure relief valves (0.5-1.2 bar activation) and ceramic separators to prevent thermal runaway. European markets require additional EN 50604-1 compliance for secondary lithium batteries. Recent updates to NFPA 505 (2023 edition) mandate automatic fire suppression systems for battery charging areas in warehouses exceeding 5,000 m².
Standard | Requirement |
---|---|
IEC 62619 | Overcharge/over-discharge protection |
UL 2580 | Crash test certification |
UN38.3 | Altitude simulation testing |
Which Industries Use 24V 60Ah Forklift Batteries?
Primary users include warehousing/logistics (85% adoption rate), manufacturing plants, and cold storage facilities. Emerging applications include automated guided vehicles (AGVs) in smart factories and airport ground support equipment. The global market for industrial forklift batteries is projected to grow at 7.2% CAGR through 2028, driven by e-commerce expansion and emission regulations.
What Are the Maintenance Requirements for These Batteries?
Lithium-ion models require minimal maintenance—avoid deep discharges below 20% and store at 40-60% charge in dry environments (15-25°C optimal). Lead-acid batteries need weekly water refills and equalization charges. Both types benefit from monthly terminal cleaning with bicarbonate solution and torque checks (8-12 N·m for terminal connections).
How Does Lithium Technology Improve Forklift Operations?
Lithium-ion batteries enable opportunity charging during breaks, increasing productivity by 18-23% compared to lead-acid. They maintain consistent voltage output throughout discharge, avoiding the 15% power drop seen in lead-acid systems. With 98% energy efficiency versus 80% in traditional batteries, they reduce electricity costs by $2,100 annually per forklift (based on 2-shift operations).
Modern lithium forklift batteries now achieve 10,000+ full cycles with proper management—triple the lifespan of lead-acid. Our clients report 23-month ROI through reduced downtime and elimination of acid spill containment costs. The latest trend is modular designs allowing 24V-80V reconfiguration for mixed fleets.”
— Redway Power Engineering Team
Conclusion
Selecting a 24V 60Ah forklift battery wholesale partner requires technical evaluation of energy density (140-160 Wh/kg for lithium), charge acceptance rates (up to 2C fast-charging), and smart monitoring capabilities. Prioritize suppliers offering ISO-certified production with localized service centers. The shift to lithium-ion reflects operational cost savings of $18,000-$25,000 over a 5-year lifecycle compared to lead-acid alternatives.
FAQ
- How long does a 24V 60Ah battery power a forklift?
- Runtime varies by load: 6-8 hours for 1.5-ton capacity models at 70% discharge depth. Lithium batteries sustain 95% capacity for first 800 cycles versus 60% in lead-acid.
- Can I replace lead-acid with lithium without forklift modifications?
- Most modern chargers support both chemistries. Verify voltage compatibility (±5% tolerance) and BMS communication protocols. Redway provides retrofit kits ensuring plug-and-play installation.
- What documentation accompanies wholesale orders?
- Expect MSDS sheets, UN38.3 test reports, CE/UL certificates, and charge profile specifications. EU shipments require DoC for Machinery Directive 2006/42/EC compliance.